Jak określić właściwe wymagania odnośnie przyrządów pomiarowych?
Jednym z najcześciej spotykanych przeze mnie problemów (i jednym z poważniejszych zarazem!) jakie identyfikuję w systemach zarządzania wyposażeniem pomiarowym jest brak właściwie ustalonych wymagań wobec stosowanych w firmach urządzeń pomiarowych. Sprawa wydaje się i jest fundamentalna, jednak w praktyce najczęściej nie jest rozwiązana wcale (serio), lub potraktowana mocno po macoszemu. W dzisiejszym wpisie podejmiemy się próby rozwiązania tego problemu a także wskażemy zagrożenia jakie niesie jego dalsze zaniedbywanie. Jednocześnie wpis ten będzie powiązany z kilkoma następnymi, które łączyć będzie wspólny mianownik, jakim jest niedopasowanie systemów zarządzania do rzeczywistych potrzeb organizacji. Póki co jednak zapraszam do lektury tekstu, który mam nadzieję pozwoli Wam określić właściwe wymagania odnośnie przyrządów pomiarowych.
System zarządzania wyposażeniem pomiarowym
Zacznijmy nieco przewrotnie. Na podstawie własnych spostrzeżeń ukułem własną definicję systemu zarządzania wyposażeniem pomiarowym, jaką zdaje się realizować wiele przedsiebiorstw:
System zarządzania wyposażeniem pomiarowym:
Zbiór procedur i zasad zmierzających do zapewnienia, że przejdziemy audyt w obszarze wyposażenia pomiarowego i pomiarów bez niezgodności…
Nie chcę zagłębiać się w postrzeganie przez firmy szerokopojętej jakości jako balastu i źródła zmartwień i wydatków, bo o tym pisałem tutaj. Skupmy się więc na systemie. Definicja powyższa odzwierciedla niestety rzeczywistość wielu firm i stoi w kompletnej sprzeczności z tym, co lubię nazywać SKUTECZNYM systemem zarządzania wyposażeniem pomiarowym:
SKUTECZNY System zarządzania wyposażeniem pomiarowym:
Zbiór procedur i zasad zapewniających, że wyposażenie pomiarowe i procesy pomiarowe są przystosowane do ich zamierzonego użycia. Ma istotne znaczenie w osiąganiu celów dotyczących jakości wyrobu i zarządzaniu ryzykiem niepoprawnych wyników pomiarów.
Powyższa definicja zaczerpnięta z normy ISO 10012 nakierowuje nas bardzo wyraźnie (jak cała znakomita norma zresztą) na istotę zagadnienia, mianowicie na przystosowanie do zamierzonego użycia (nota bene ISO 9001 również). Łatwo domyślić się, że zamierzone użycie będzie różne dla różnych przemysłów, przedsiębiorstw a nawet procesów wewnątrz jednego przedsiębiorstwa. Natychmiast nasuwa się także kolejny wniosek i jednocześnie moje pytanie – skoro tak, to na jakiej podstawie powszechnie przyjmuje się wymagania norm na przyrządy pomiarowe jako właściwe do naszych zastosowań? Czujecie, że coś tu nie gra?
Źródła problemu
Przyczyn takiego stanu rzeczy wskazać możemy co najmniej kilka:
- brak dostatecznej wiedzy w tym obszarze wśród kadry odpowiedzialnej za proces
- brak chęci doskonalenia – system z konieczności, żeby pozyskać klienta lub przerośnięte ego organizacji („robimy tyle lat i było dobrze”)
- słaba świadomość firm wdrażających systemy zarządzania w tym konkretnym obszarze (więcej tutaj)
- brak ustalonych jasnych wytycznych
- bałagan w normach i przewodnikach
- powtarzane „z pokolenia na pokolenie” błędne teorie i założenia
Przyczyny te należy rozpatrywać nie tylko w kontekście tematu dzisiejszego wpisu, ale znacznie szerzej – jako przyczyny funkcjonowania „byle jakich” systemów zarządzania.
Zagrożenia
Główne zagrożenie jakie powoduje brak właściwie określonych wymagań odnośnie wyposażenia pomiarowego jest zbieżne z podstawowym problemem zarządzania jakością odnośnie wyrobów, mianowicie:
- dopuszczamy urządzenia pomiarowe, które nie powinny zostać dopuszczone
- odrzucamy urządzenia pomiarowe, które mogłyby zostać dopuszczone
Konsekwencje płynące z tego procederu mogą być różne w zależności od rodzaju przemysłu, wyrobu itd., ale finalnie da się je sprowadzić do wspólnego mianownika jakim są (ponownie kłaniają się fundamenty zarządzania jakością):
- nadmierne koszty jakości
- koszty braku jakości
Czyli upraszczając – pieniądze i ewentualnie długofalowo wizerunek marki.
Problem
Jak wskazałem na wstępie dwie najpoważniejsze sytuacje, jakie spotykam w kontekście wymagań, a na których chciałbym się skupić to:
- brak ustalonych wymagań
- niewłaściwie ustalone wymagania
W przypadku pierwszym w organizacji nie ustalono wymagań wobec przyrządów pomiarowych w ogóle. Organizacja liczy, że to laboratorium wzorcujące lub dostawca narzędzia określi wymagania i zapewni ich spełnienie. Przekroczenie wymagań według takich systemów zarządzania następuje w chwili gdy laboratorium zewnętrzne poinformuje o tym fakcie na świadectwie lub w momencie uszkodzenia urządzenia.
Przypominam: laboratorium zewnętrzne w domyśle nie orzeka o zgodności z wymaganiami! Robi to na życzenie klienta (z kilkoma wyjątkami). Więcej tutaj.
Generalnie przyjąć można zasadę, że jeśli nie ma wymagań, to wszystko jest zgodne. Brzmi wygodnie, ale w rzeczywistości jest odpalonym już lontem dynamitu, który może być różnej długości, ale w końcu dotrze do celu i zaowocuje potężną reklamacją. Aby nie być gołosłownym przedstawię pochodzący z ISO 10012 diagram obrazujący proces realizacji potwierdzenia metrologicznego:
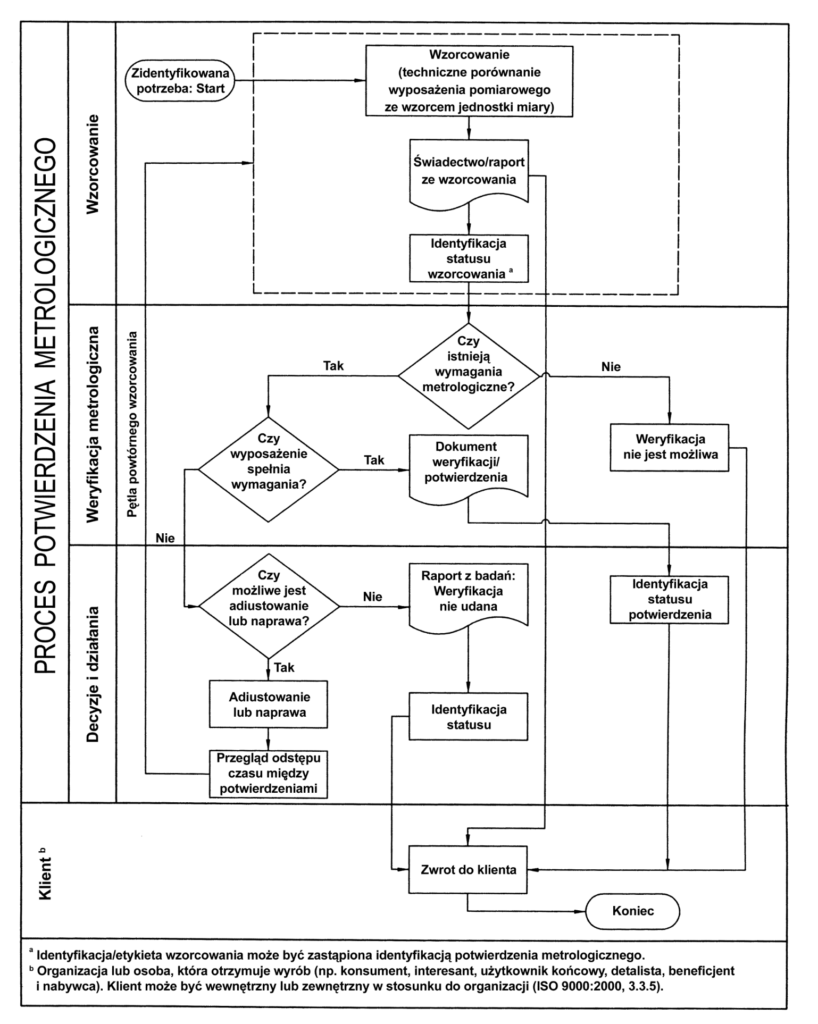
Zwróćmy uwagę na etap weryfikacji metrologicznej i pierwszy punkt decyzyjny. Komentarz wydaje się zbędny.
Drugi przytoczony przypadek – wymagania są, ale niewłaściwe. Najczęściej wymaganiami tymi są wymagania stosownej normy (jeśli jest) lub dokumentacja producenta. Pozornie więc podwórko wydaje się być zagospodarowane, ale przypominam jak kwestia wymagań formułowana jest przez normy: mają być przystosowane do zamierzonego użycia (Jeżeli chodzi o same wymagania, mogą one być naturalnie różne, ale my skupimy się dalej dla uproszczenia na błędzie wskazania). Przytoczyć w tym miejscu warto kolejną podstawową zasadę, mianowicie:
Wymagania (pożądane błędy, dokładność…) nie mogą być ustalone ani ocenione w oderwaniu od zamierzonego użycia. Podobnie sama „dokładność” – o tym, czy przyrząd jest „dokładny” czy nie decyduje jego przeznaczenie.
Czy 0,01 mm błędu to dużo czy mało? Zależy. W precyzyjnej obróbce metali – może być dużo. W budowlance – kosmicznie mało. Widzimy więc wyraźnie, że wymagania ustalić musimy sami odnosząc je (w uproszczeniu) do wymagań naszych procesów pomiarowych. Dlaczego nie zadziała zastosowanie norm ani dokumentacji technicznej producenta? Wymagania określone w normie traktujmy jako przeznaczone dla producentów sprzętu pomiarowego. Muszą być, aby klient wiedział czego się spodziewać. Nadmienić należy, że są one dość restrykcyjne i właśnie dlatego część firm będzie odrzucała narzędzia niespełniające wymagań normy jako niezdatne dla siebie, chociaż często mogłyby z powodzeniem realizować ich zadania pomiarowe. Tu świetnym przykładem niech będzie ISO 13385-1, która jasno zaznacza to na wstępnie mówiąc o weryfikacji (przez producenta, sprzęt nowy) i reweryfikacji (u klienta, podczas kolejnych sprawdzeń). Innym aspektem niewłaściwych wymagań jest stosowanie wymagań nieaktualnych. Świat nie stoi w miejscu, narzędzia rozwijają się, znikają z norm niskie klasy dokładności (przykładem niech będą liniały krawędziowe wg DIN 874 – jeszcze niedawno było kilka klas, aktualnie mamy jedynie 00). Porównajmy zresztą wymagania odnośnie suwmiarek z dzienników GUM (wycofane w roku 2000, w wielu firmach stosowane nadal) z aktualną normą:

Właściwe wymagania odnośnie przyrządów pomiarowych.
Jak zatem dopasować wymagania odnośnie przyrządów pomiarowych do zamierzonego użycia? Metod jest kilka, ja nie chcąc pisać tu elaboratu przybliżę je pokrótce.
Idea wszystkich metod jest najogólniej mówiąc taka, aby zachować odpowiednią relację między błędem wskazania narzędzia (w profesjonalnym ujęciu: rozszerzoną niepewnością pomiaru U, ewentualnie zmiennością procesu w przypadku MSA) a tolerancją mierzonego wymiaru (T). Powszechnie uznaje się, że U (w uproszczeniu na nasze potrzeby MPE, MPL) nie powinno przekroczyć 10%T (zasada przytaczana kilkakrotnie, odsyłam choćby tutaj). Zapewnia to odpowiednią jakość decyzji. Inaczej mówiąc: im mniejszym „fragmentem” przedziału tolerancji jest niepewność pomiaru, tym mamy większe pole manewru, lepiej i pewniej oceniamy wynik pomiaru. Ponieważ 10% nie zawsze jest możliwe do osiągnięcia, można przyjąć progi warunkowe, np. 20, 25 czy 30%. Pamiętajmy jednak, że wraz z pogarszaniem się relacji U vs T spada jakość naszych decyzji, co można zobrazować jak niżej:

Kryteriami możemy także żonglować w odniesieniu do istotności (krytyczności) mierzonego wyrobu czy wymiaru, np:
Stosunek błędu przyrządu do przedziału tolerancji T powinien być nie większy niż: 1:10 (10%) dla wymiarów krytycznych i istotnych oraz 1:4 (25%) dla wymiarów mniej znaczących (minor).
Druga metoda jest powszechnie stosowana w branżach automotive i aerospace (oczywiście nie tylko) i nosi nazwę MSA – Measurement System Analysis. Zadaniem MSA jest praktyczna analiza procesu pomiarowego, pozwalająca poznać i zrozumieć zakres jego rzeczywistej zmienności w warunkach docelowych. Na podstawie eksperymentalnie uzyskanych danych liczbowych możliwe jest dokonanie właściwej oceny zdolności procesu pomiarowego względem wymagań. W celu wykonania oceny zdolności procesu stosuje się najczęściej analizę powtarzalności i odtwarzalności (GAGE R&R, Repeatability and Reproductibility). MSA jest metodą bardziej praktyczną niż wybitnie analityczna niepewność pomiaru. Pozwolę sobie jednak nie rozwodzić się dalej na temat samego procesu MSA, gdyż poświęcam mu osobny wpis, który na blogu pojawi się już za tydzień.
Konkluzja
Jak widać z pozoru prosty temat na odpowiednim poziomie wtajemniczenia może stać się zaawansowanym i złożonym procesem. Naszym najlepszym narzędziem jest tak naprawdę nasze własne doświadczenie, oraz oczywiście znajomość i umiejętność stosowania pewnych sprawdzonych metod. Naszym celem z punktu widzenia systemów zarządzania powinno być w każdym razie ustalenie własnych, dopasowanych do rzeczywistych potrzeb wymagań odnośnie narzędzi pomiarowych, co pozwoli na trzymanie w ryzach kosztów jakości i braku jakości. Osobiście uważam, że świadomość dobrej organizacji w tym obszarze daje sporo satysfakcji i zapewnia spokojny sen.
Do następnego!
Opublikuj komentarz
Musisz się zalogować, aby móc dodać komentarz.