Przyrządy do pomiaru płaskości i prostoliniowości w dużej skali
Rozwój technik współrzędnościowych i optycznych, zwłaszcza ramion pomiarowych i trackerów spowodował, że kiedy zachodzi potrzeba zmierzenia cech geometrycznych typu płaskość czy prostoliniowość na dużym obiekcie, w pierwszej kolejności kierujemy uwagę właśnie ku tym urządzeniom. Wciąż jednak – czy to z powodów ograniczeń budżetowych czy charakteru zadania pomiarowego (w tym trudnych warunków spowodowanych np. przez zanieczyszczenie otoczenia) – techniki te nie zawsze dają się zaimplementować. Warto wtedy wiedzieć, że dostępne są także inne, niekoniecznie zgrubne czy archaiczne w oczach niektórych rozwiązania.
Dziś przedstawię mniej i bardziej znane metody wykorzystujące przyrządy do pomiaru płaskości umożliwiające pomiary dużych obiektów.
Pomiar płaskości i prostoliniowości liniałami
Na początek do tablicy wywołamy dobrze znaną warsztatową metodę porównawczą wykorzystującą liniały. Warto przy tej okazji przywołać ważną zasadę umożliwiającą uzyskanie właściwych pomiarów nie tylko liniałami:
Powierzchnie najlepiej sprawdzać krawędzią, krawędzie najlepiej sprawdzać powierzchnią
Z jednej strony chodzi o wyeliminowanie elementu ekwilibrystyki jakim jest próba umieszczenia np. liniału krawędziowego na innej krawędzi, z drugiej – o zniwelowanie wzajemnego oddziaływania na siebie dwóch nieidealnych płaszczyzn, co w niektórych przypadkach fałszuje lub uniemożliwia pomiar w ogóle. Dzieje się tak np. przy próbie oceny szerokości szczeliny świetlnej gdy przylegające powierzchnie zasłaniają prześwit. Z tego powodu do wzorcowania kątowników stosuje się kątownik walcowy złożony z nieskończonej ilości tworzących będących krawędziami, a nie kątowniki powierzchniowe czy choćby granitowe.
Zatem:
- chcąc sprawdzić prostoliniowość na walcu posłużymy się liniałem powierzchniowym (obiekt: krawędź – wzorzec: powierzchnia)
- chcąc sprawdzić płaskość czy prostoliniowość na powierzchni posłużymy się liniałem krawędziowym (obiekt: płaszczyzna – wzorzec: krawędź)
Idealnie jeśli długość wzorca jest większa niż sprawdzanego obiektu. I tu pojawia się problem: najdłuższe dostępne liniały krawędziowe produkowane są do 1500 mm. Liniały powierzchniowe oferują już znacznie większe długości: „z półki” bez problemu do 3000 mm, na zamówienie i 6000 mm, w tym granitowe, które potrafią na tej długości zaoferować odchyłkę płaskości rzędu kilkunastu mikrometrów.
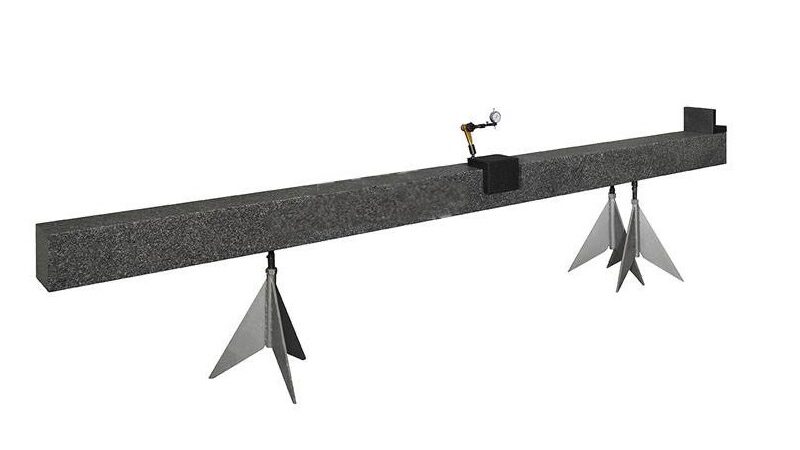
W zależności od jakości powierzchni i samego obiektu wyznaczenie odchyłki odbywa się albo przez ocenę szerokości szczeliny świetlnej (tzw. metoda „na prześwit”, małe obiekty, odchyłka nieprzekraczająca okolic 3 µm) albo – co bardziej powszechne w tej skali – przez wykorzystanie szczelinomierza płytkowego. Liniał opiera się zawsze w najwyższym punkcie, następnie umieszczając kolejno płytki szczelinomierza szukamy największej odchyłki w kierunku ujemnym (zagłębienia) na całej długości. Z racji stopniowania kolejnych płytek zwykle co 0,05 mm taką też należy przyjąć zdolność oceny – bliżej dziesiątych niż setnych części milimetra…
Chcąc zachować zgodność ze sztuką liniał powinno oprzeć się na płytkach wzorcowych rozmieszczonych w tzw. punktach Granta (rozmieszczonych od krawędzi z obu stron od 0,2232 x L) aby zminimalizować ugięcie.
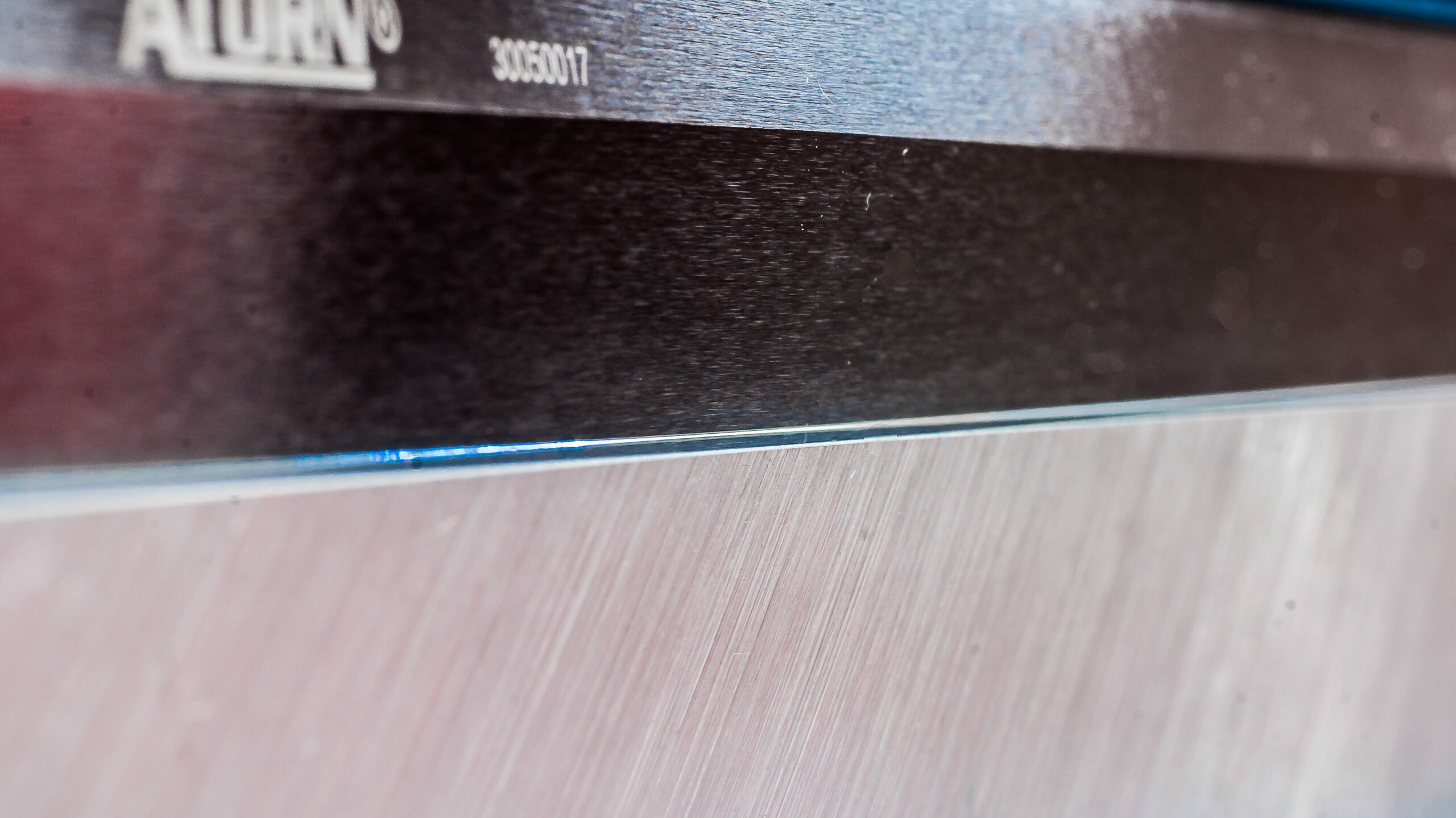
Przyrządy do pomiaru płaskości i prostoliniowości
Na rynku spotkać można ciekawe rozwiązania umożliwiające pomiar ze znacznie lepszą dokładnością, dodatkowo cyfrowe, a więc umożliwiające precyzyjniejsze odwzorowanie profilu wykorzystując większą ilość punktów pomiarowych. Jednym z ciekawych przykładów są urządzenia MICROTECH występujące w wersjach 1D (tylko pomiar odchyłki w kierunku Z – pionowym) oraz 2D – mierzące także odległość w osi poziomej X.
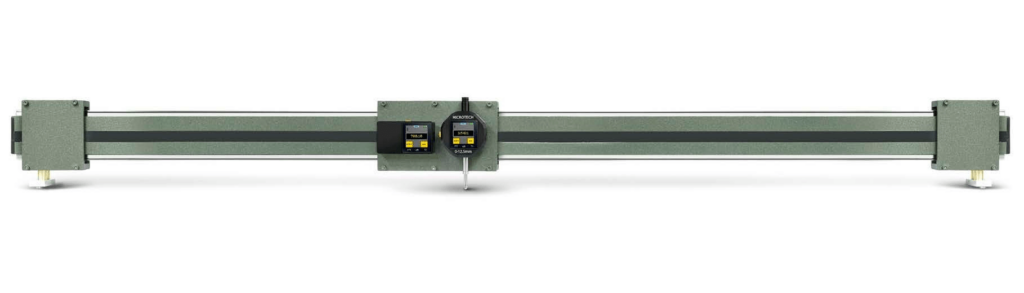
Na prowadnicy zamontowany jest cyfrowy czujnik długości (zakres 12/25 lub 50 mm), który odpowiada za interesujący nas pomiar wysokości. Dzięki połączeniu bezprzewodowemu i wyzwalaczowi czasowemu możemy bardzo wygodnie zgromadzić znaczną ilość punktów pomiarowych. Od niedawna urządzenie występuje także w opcji z sondą laserową. Producent oferuje modele o zakresach od 900 do 3800 mm. Metoda ta zdecydowanie bardziej zbliża nas do pomiaru w setnych lub nawet tysięcznych częściach milimetra.
Zaawansowane systemy do pomiaru płaskości i profilu
Rozwiązaniem z górnej części skali jakościowej i cenowej są systemy dedykowane do pomiaru płaskości czy kształtu profilu wykorzystujące laserowe głowice pomiarowe. W dużej skali wiodące na świecie są produkty marki SCANTRON z Wielkiej Brytanii. Flagowy model – PROSCAN MAGNUM może mierzyć naprawdę duże arkusze zarówno jako samodzielne stanowisko jak i w linii produkcyjnej. Przykładem zastosowania może być pomiar blachy po rozwinięciu ze zwoju. Zachowuje przy tym więcej niż wystarczającą dokładność, bez problemu osiągając wartości błędu rzędu mikrometra.
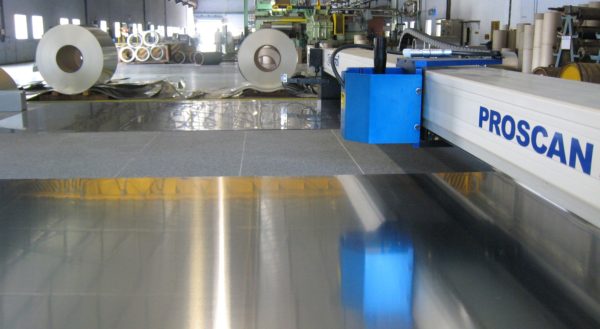
Pomiary na płycie granitowej z wykorzystaniem wysokościomierza
Dysponując odpowiednio dużą płytą pomiarową zadanie możemy zrealizować stosując ją jako podstawę – bazę, natomiast pomiar wykonać z wykorzystaniem wysokościomierza suwmiarkowego lub jeszcze lepiej -cyfrowego na poduszce powietrznej. Pierwsza opcja skłania raczej do pomiaru w sposób punktowy, druga umożliwia pomiar w sposób ciągły (skaning), urządzenia tego typu posiadają najczęściej wbudowany do wyznaczania odchyłki prostoliniowości algorytm.
Wyznaczając odchyłkę płaskości lub prostoliniowości tą metodą pamiętajmy o odpowiednim bazowaniu detalu tak, abyśmy mierzyli faktycznie odchyłkę od płaskości a nie zmiany grubości powierzchni…
Aby prawidłowo zrealizować taki pomiar, musimy wpierw właściwie zdefiniować odchyłkę od płaskości. W ujęciu geometrycznym GD&T (Geometric Dimensioning and Tolerancing) i technik współrzędnościowych odchyłką od płaskości jest różnica pomiędzy dwiema równoległymi płaszczyznami opisanymi na płaszczyźnie mierzonej (analogicznie definiujemy prostoliniowość, z tym że operujemy prostymi w 2D a nie trójwymiarową płaszczyzną):
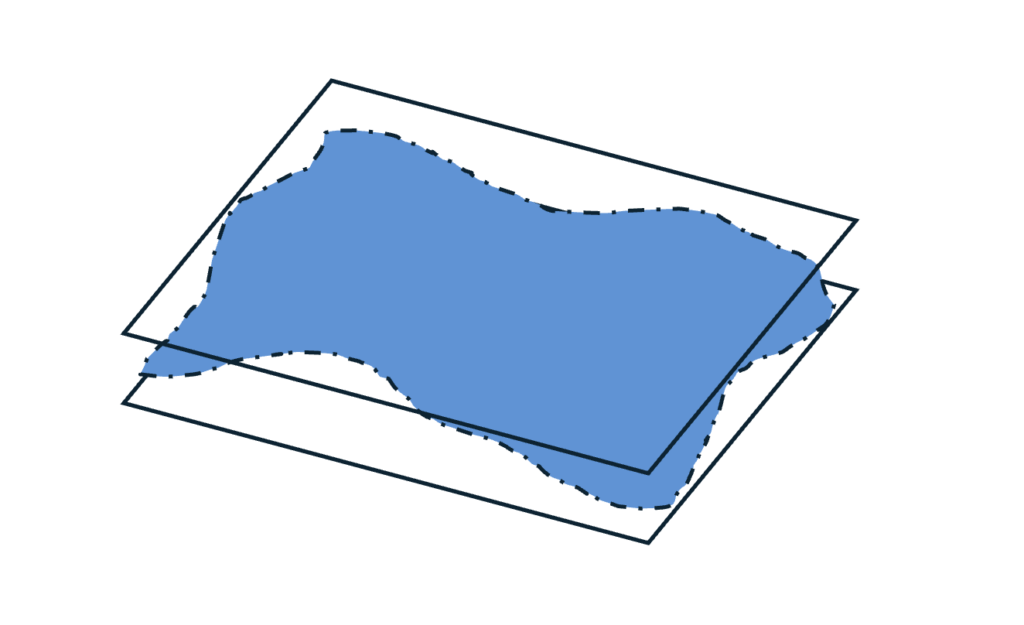
Dopuszczalna odchyłka od płaskości jest więc niczym innym jak odległością między dwiema płaszczyznami, między którymi ma się zmieścić płaszczyzna badana. Aby badać płaskość w ten sposób techniki współrzędnościowe okazują się idealnym narzędziem, gdyż oprogramowanie na podstawie zebranych punktów sporządzi trójwymiarowy model płaszczyzny, który łatwo odniesie do wymagań. Pomiar ten będzie zawsze niezależny i nie ma ryzyka, że wynik zostanie zafałszowany przez np. grubość materiału.
Aby prawidłowo zrealizować taki pomiar metodami dwuwymiarowymi musimy zadbać o właściwą realizację bazy. Jeśli konieczne – zastosować podparcie w odpowiednich punktach, aby wyeliminować choćby wpływ wypływek przy pomiarze detali z tworzyw sztucznych, na co ponownie uczulam. Popularny pomiar płaskości przez położenie detalu na płycie i szukanie „maxa” często kończy się pomiarem nie tego, czego oczekujemy.
Zwracam też uwagę, że punktowy pomiar bez budowania modelu płaszczyzny będzie najczęściej różnicą między wartością maksymalną a minimalną z kilku pomiarów, co bez odpowiedniej realizacji bazy nie jest tym samym co odchyłka płaskości definiowana przez tolerowanie geometryczne.
Pomiary z wykorzystaniem poziomnicy, (auto)kolimatora lub interferometru
Ciekawą i precyzyjną metodą wyznaczania odchyłki od płaskości dużych powierzchni może być także zastosowanie poziomnicy precyzyjnej (maszynowej, a jeszcze lepiej elektronicznej), ewentualnie lunety kolimacyjnej. Obie metody są z powodzeniem stosowane podczas wzorcowania płyt pomiarowych, zwłaszcza granitowych. Obie oferują także podobny poziom poprawności i precyzji.
Przykładem niech będzie poziomnica elektroniczna z przełączaną podziałką, która pozwala na pomiar odchylenia od poziomu rzędu 0,001 mm/m. Metoda polega na wykonywaniu odchyleń od poziomu w odcinkach równych długości podstawy urządzenia, np. 200 mm. Mierzone są różnice między kolejnymi pozycjami poziomnicy w przekrojach badanego elementu. Z przekrojów budowana jest następnie siatka a to z kolei pozwala na zbudowanie trójwymiarowego modelu powierzchni.
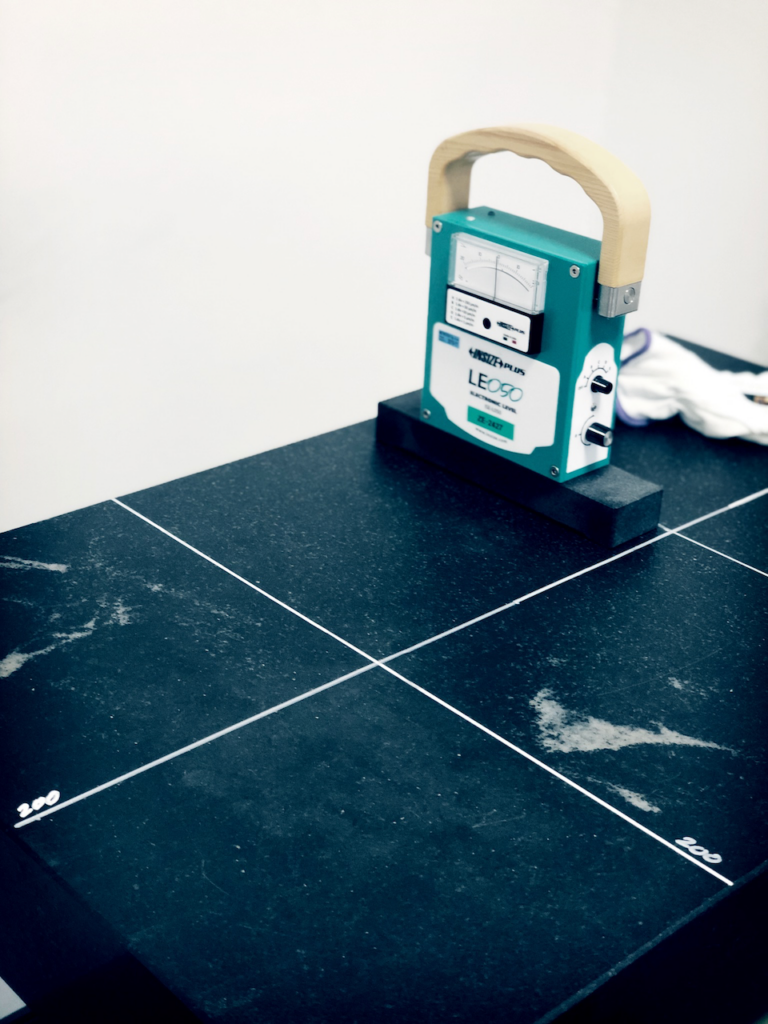
O tym, czy tak wysoką czułość da się zastosować w praktyce decydują naturalnie wypoziomowanie i docelowa odchyłka badanego obiektu… Czasem wystarczy i poziomnica maszynowa z działką 0,02 mm/m. Największa zaleta metody jest jednocześnie największą jej wadą – o ile daje dobry obraz dużej powierzchni, o tyle nie jest w stanie uwzględnić odchyłek mikro typu ubicia.
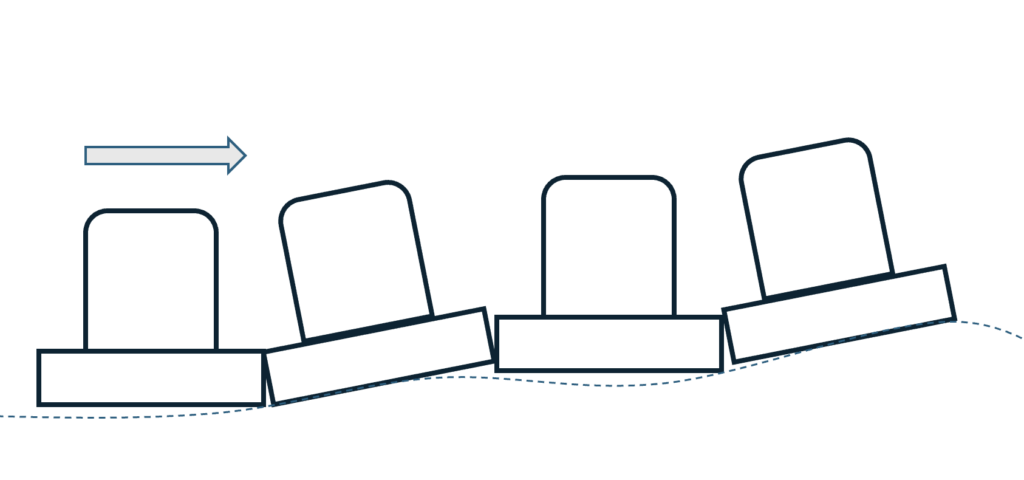
Efektem naszych pomiarów będzie zbiór wartości zmierzonych w siatce przekrojów, która to też może przybrać różne kształty. Mamy kilka podejść do sposobu rozmieszczania kolejnych pomiarów, najczęściej jednak wystarczającym jest układ zbliżony do poniższego:
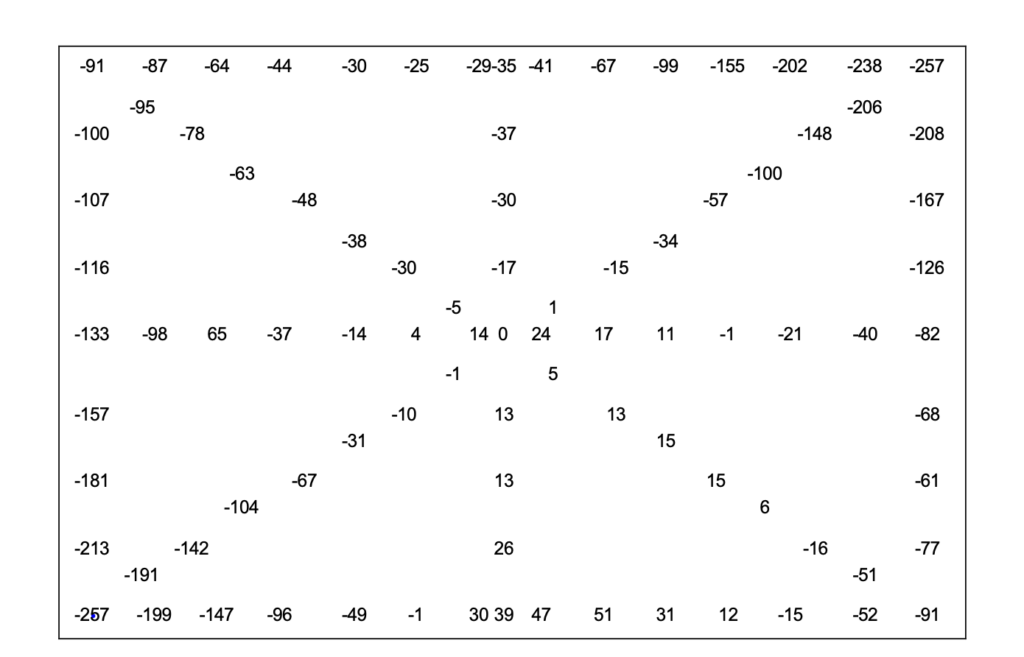
Warto wesprzeć się oprogramowaniem, które pomoże nam w transformacji wyników w model płaszczyzny (np. WPlan firmy Microplan). Przywołane w nagłówku pozostałe przyrządy do pomiaru płaskości – z wykorzystaniem kolimatora czy interferometru laserowego są co do zasady podobne, oferując jeszcze wyższą poprawność. Sam temat kalibracji płyt pomiarowych to jednak temat na osobny artykuł, przy okazji którego przedstawię więcej szczegółów.
W tradycyjnej metrologii warsztatowej znana była także metoda „na farbę” – tuszowanie. Nierówności powierzchni wykrywało się poprzez naniesienie cienkiej warstwy farby na powierzchnię wzorcową i rozcieranie po powierzchni badanej tak, aby uzyskać odbicie farby na wzniesieniach.
Na koniec
Niezależnie od wybranej metody w pomiarach płaskości da się wskazać jeden czynnik krytyczny decydujący o poprawności przedsięwzięcia: jest to właściwe określenie bazy i ustalenie odniesienia w postaci punktu zero. Nic nowego i każdy, kto miał okazję szkolić się ze mną wie jaki nacisk kładę na zrozumienie menzurandu i określenie właściwej metody. Dopiero potem myśleć można o sprzęcie – nie na odwrót…
Opublikuj komentarz
Musisz się zalogować, aby móc dodać komentarz.